Preventive Maintenance powered by Machine Learning
TDM solutions collects data, analyses it, predicts faults and forecasts optimal schedule for maintenance.SPECIFICS of Fault Prediction
Preventive maintenance generally includes two tasks: fault prediction and optimization model development which predicts optimal schedule for maintenance activities. Optimization model analyzes current equipment load, working schedule, new equipment purchase schedule. The model evaluates risks related to equipment failure and downtime. Faults are forecasted using both historical and real-time data.
Why is Preventive Maintenance Important?
Preventive maintenance is crucial for high-load systems. For example, in the airline and railway industry late equipment repair and maintenance can not only impose financial costs but also cause lethal accidents.
Data Driven Predictive Maintenance
The more sources of data are used to identify patterns, the higher the accuracy of failure prediction is achieved. Clues can be found in the most unexpected sources.
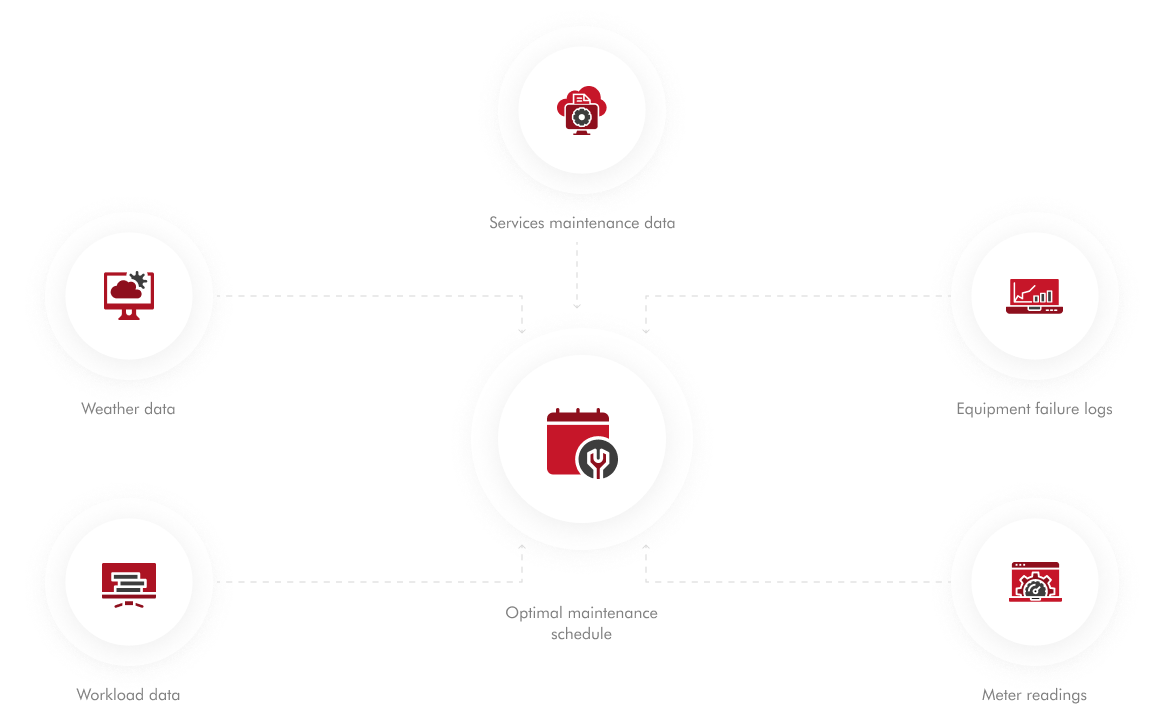
Benefits of Predictive Maintenance

Increase equipment life cycle and improved performance

Safe working conditions for a reliable employer brand image

Decreased maintenance costs, saving on consumables and spare parts (oil, gas, etc.)

Reduced equipment downtime period

Prevented lawsuits and reduced legal costs

Optimized maintenance schedule
Contact Us Now!
Do you want to introduce predictive maintenance to your business and cut related costs?
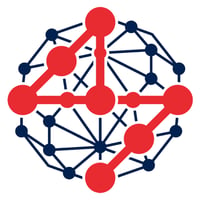
Transforming Businesses Globally Through Generative AI
Arshad K. (Founder)